Crafted from renewable, biodegradable wool for a smaller environmental footprint.
Resists settling and consistently maintains performance over time.
Superior thermal and acoustic properties ensure consistent year‑round comfort.
Better Insulation, Naturally
Premium Wool, Proven Performance
We use high-quality fibers for insulation that’s naturally effective, safe, and built to last.
Precision-Engineered for Quality
Our process enhances wool’s natural benefits, delivering high performance and lasting durability.
Sustainable by Design
From ethically sourced fibers to biodegradable materials, every step reduces environmental impact.
Comfort in Every Season
Regulates temperature, absorbs sound, and keeps your space quiet and cozy year-round.
$75.00
- Unit price
- / per
In stock
Havelock Wool Sound and Indoor Air Quality Panel - 2"
$185.00
- Unit price
- / per
$185.00
- Unit price
- / per
In stock
$48.00
- Unit price
- / per
In stock
$150.00
- Unit price
- / per
In stock
$75.00
- Unit price
- / per
In stock
$150.00
- Unit price
- / per
In stock
$180.00
- Unit price
- / per
In stock
$95.00
- Unit price
- / per
In stock
$0.00
- Unit price
- / per
In stock
$185.00
- Unit price
- / per
In stock
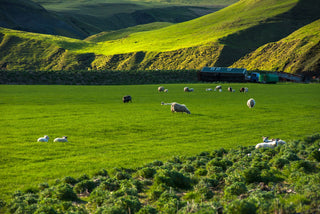
Ready to make the natural choice?
Join the movement towards healthier, more sustainable living with Havelock Wool.
Since installation over our attached garage 2 years ago, it is no longer uncomfortably hot in the summer or too cold in the winter. We have noticed that our overall electric bill has decreased during those two seasons as well.
Always great doing business with you. Your wool insulation is exceptional and I am delighted to have it in the ceilings, floors, and walls of my small retreat space. It is like being wrapped in a shawl.
Our clients discovered Havelock Wool online. They are trying to do as healthy a restoration as possible. We all were very surprised how easy it was to deal with Havelock. We all got a kick out of our first wool insulation project and are looking forward to more!
I have been a Green builder for years now, I am truly impressed how clients ‘feel’ the difference in their bedrooms.
The rumors are true, this stuff is actually fun to work with! I chose Havelock for my van as it is toxic free, renewable, sustainable, improves air quality, absorbs sound and OUTPERFORMS a lot of other popular insulation materials.
This building has been transformed simply by adding 5.5 Havelock wool batts. The outside noise from 17th St. is gone, the ring of construction on the property is more of a vibration and the inside of the building just feels right. This insulation should be a standard.
I’m so glad I went with a natural product like this for my van. The stuff really is good quality stuff. Natural is the way to go, you dont want to be cooped up in a metal can, in the summer and your insulation is emitting toxic fumes in your home.
Frequently Asked Questions
Curious about wool insulation? Explore answers to some of the most common questions about Havelock Wool, its benefits, and how it compares to other insulation options.
Wool insulation is a natural, sustainable alternative to traditional materials like fiberglass or foam. It offers superior thermal performance, naturally regulates humidity, and improves indoor air quality, all without harmful chemicals.
Yes! Wool insulation is 100% renewable, biodegradable, and ethically sourced. Choosing wool reduces your environmental impact while supporting sustainable practices.
Wool naturally absorbs and releases moisture without losing its insulating properties. This helps prevent mold and mildew, making it ideal for homes, vans, and studios.
Absolutely. Wool’s dense, fibrous structure makes it excellent for acoustic control, reducing noise transfer between rooms or from outside. Perfect for studios and sound-sensitive spaces.
Yes! Havelock Wool is completely non-toxic and free from harmful chemicals, making it a safe choice for creating a healthy living environment.
With proper installation, wool insulation can last for decades. Its natural durability and resilience ensure long-term performance, making it a smart, sustainable investment.
Sustainable insulation materials include wool, cellulose, cork, and recycled denim. These natural and eco-friendly options reduce environmental impact, improve energy efficiency, and often avoid harmful chemicals found in traditional insulation.
Proper insulation is key to energy efficiency. It prevents heat loss in winter and keeps your home cool in summer, reducing reliance on heating and cooling systems. This not only lowers energy bills but also minimizes your carbon footprint.
When choosing eco-friendly insulation, prioritize materials that are renewable, biodegradable, and free from harmful chemicals. Certifications like LEED or WELL can help ensure your choice aligns with sustainable building standards