We got this in an email from a home builder just last week…
“We do a lot of work in-house but have always sub’d out insulation. Our projects are done mostly with cellulose and the installer I use is so backed logged and I’m not happy with his work lately so I wanted to explore other options. I’m skeptical of blowing in dense-packed cellulose ourselves because I was worried about not getting the correct density and the product settling over time. My understanding is that wool does not have that issue and is more forgiving in the sense that a non-professional insulation installer can blow in wool and achieve a good result with no issues in the future. Is that correct?”
The short answer is an emphatic Yes. But importantly there are two issues that make our blown-in wool insulation way more accessible to the non-dedicated installer.
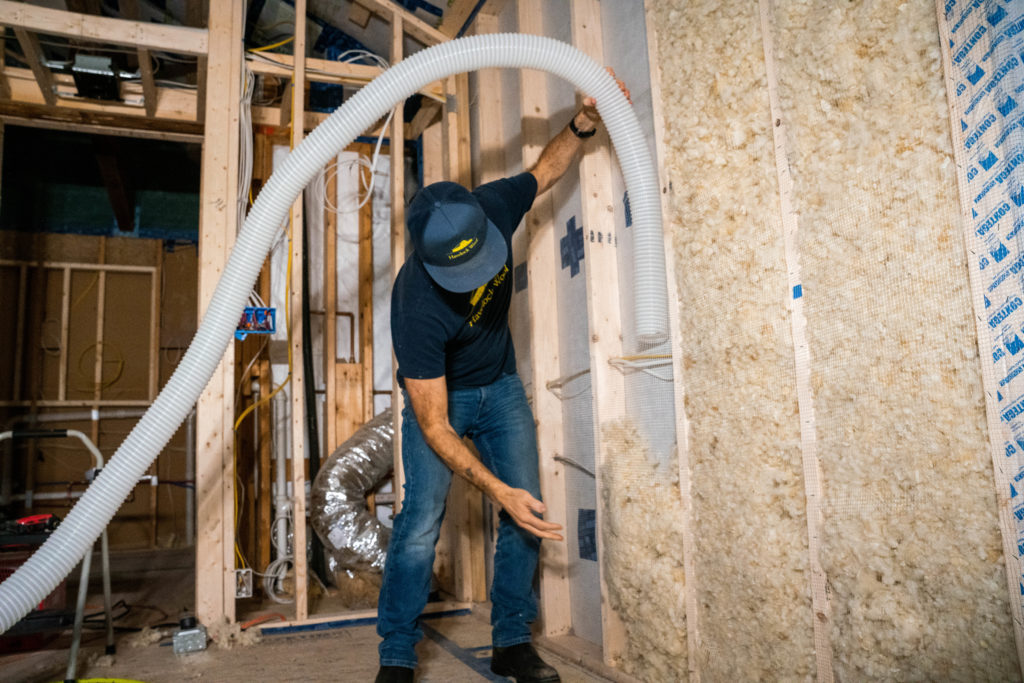
Let’s start with the fiber.
Wool is very different than any other type of insulation. In an ingenious display of evolution the inside of a wool fiber, the cortical cell, is actually arranged in two distinct halves. These two halves respond differently to the environment which makes the wool fiber bend or crimp. This crimp is crucial because it creates bulk and traps a large volume of air between the fibers. And this makes for a good insulator. The outside of the fiber features overlapping scales called cuticle cells. The cuticle cells provide a strong exterior, protecting wool from damage. Importantly, these scales grab each other and everything around it – framing, sheathing, etc – which holds it up in the cavity, resisting compression and therefore preventing slumping. Wool also expands a bit as it manages moisture, filling up the cavity rather than sagging under the weight of moisture like synthetic alternatives.

This all translates to a natural buoyancy of the wool fiber, especially in comparison to other types of blown-in insulation, like cellulose. The data is rather striking: our blown-in requires a density of only 1.13 lbs per cubic foot which achieves an R-Value per inch of 4.3. Dense-packed cellulose is at least 3lbs per cubic foot with R-Value of 3.5-3.8. Put into even simpler terms, you need many more pounds of insulation within your wall and even then it does not insulate as well as wool. And if you miscalculate density, you’re short on desired R-Value and settling is more of a risk.
So when you go to install our blown-in wool insulation, you are indeed offered a lighter, more forgiving fiber with a superior R-Value. You’re also installing a lot less weight with a material that naturally resists compression. Oh and it’s also way cleaner.
Now let’s talk about trends in home building
“We do a lot of work in-house but have always sub’d out insulation…. the installer I use is so backed logged and I’m not happy with his work lately so I wanted to explore other options”
This message from a home builder is becoming more common. We field calls and emails every day from forward-thinking builders and contractors that want to work with healthy, high-performance materials. Often it is at the request of the homeowner but increasingly we hear of the trade initiating the conversation. And when they learn about the differences in installation, particularly for insulation, often the builder or contractors themselves are interested in doing the job. This also means that they no longer have to rely on or manage subs for what is a crucial part of the home build. As wool is a natural insulator and a healthy fiber one need not be afraid of the work, nor do you need massive amounts of training and equipment. Havelock is properly tested and certified so inspectors and fire marshals love us. Best of all, there are no call backs, as wool does what it is supposed to… insulate the house and create a healthy, high-performance and comfortable home.